Shortage of Raw Materials in the Plastic Industry
Due to the Covid-19 pandemic situation, we have been involved in a “domino effect” that has hit the world economy. This has been joined by an extreme weather of events and adverse force majeure situations that do not usually coincide in time, such as the blockade of the Suez Canal, fires or a shortage of containers.
This unusual “cocktail” of scenarios has brought global consequences in the industry sector, such as the lack of raw materials, the scarcity of which predicts fatal results for thousands of companies and millions of users.
The plastics sector is no exception, being tremendously affected by the rise in the price of raw materials and even the current shortage of these.
The reasons are various, but the main one is attributed to the reduction in fuel consumption and its consequent decrease in oil extraction, causing there to be less naphtha, less ethane, and less ethylene.
How to combat the shortage of plastic raw material?
The shortage of plastic raw material is a problem that we will have to deal with until the market stabilizes. As a more effective solution, it is proposed to use recycled plastic thanks to the property of thermoplastics that allows them to be reused several times.
This alternative is not only fueled by the lack of supply of raw materials, but there are other issues on the table such as the circular economy, sustainability, caring for the environment and the fight against climate change.
However, the progressive loss of thermoplastic’s properties as they are reused makes it impossible to use recycled materials to manufacture parts that require those properties for their use. This drawback leads us to the pertinent need to use new polymers that, with the current situation, we have to learn how to optimize them so that the lack and the extra cost of the raw material affects us to a lesser extent.
How can we optimize plastic consumption?
The consumption of plastic in the manufacturing process isn’t limited only to the material that makes up the part itself, but we must also count on the consumption of plastic destined to the waste of material (injection channels, parts with tare, incomplete parts, injection tests, wrong parts ...).
Reducing this waste is achieved by investing in the quality of the injection process.
To do this, having a high-quality mold with the ideal geometry at all levels, the relevant materials, hardness, finishes, accessories ... allows the manufacturer to minimize errors and reduce the consumption of raw material by wastage up to 30% and increase the production up to 30%. At the same time, the efficiency in the injection process will also bring us savings in electricity consumption, the price of which is currently exorbitant.
At Santos & Schulz we have been committed for more than 20 years to the excellence of our molds and services. Our exhaustive quality control allows our clients to receive their molds once they have passed a series of controls and tests so that the resulting piece is simply perfect. In this way, when you receive the mold, you just have to install it in your injection machine and start producing in an optimized way.
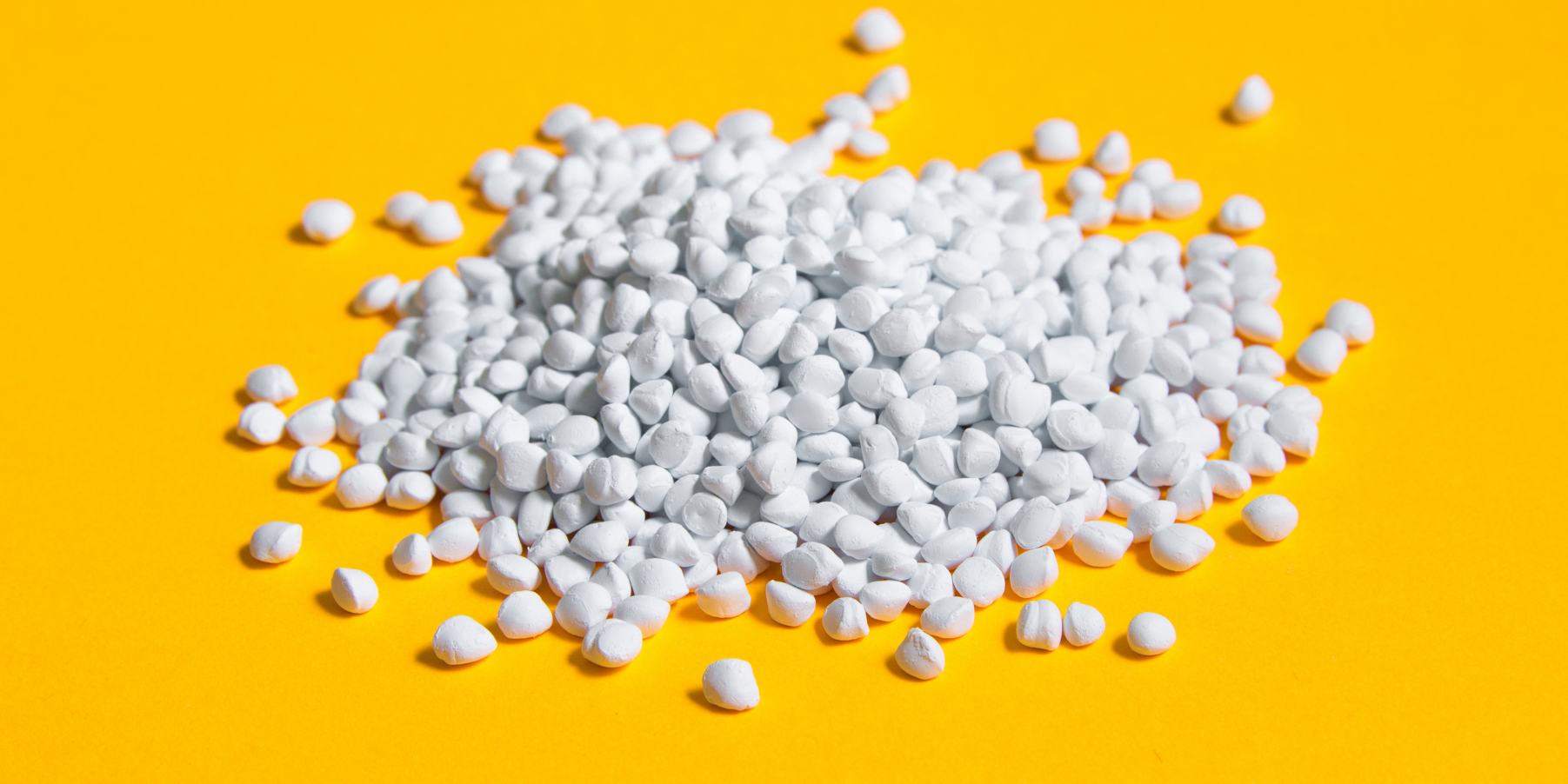